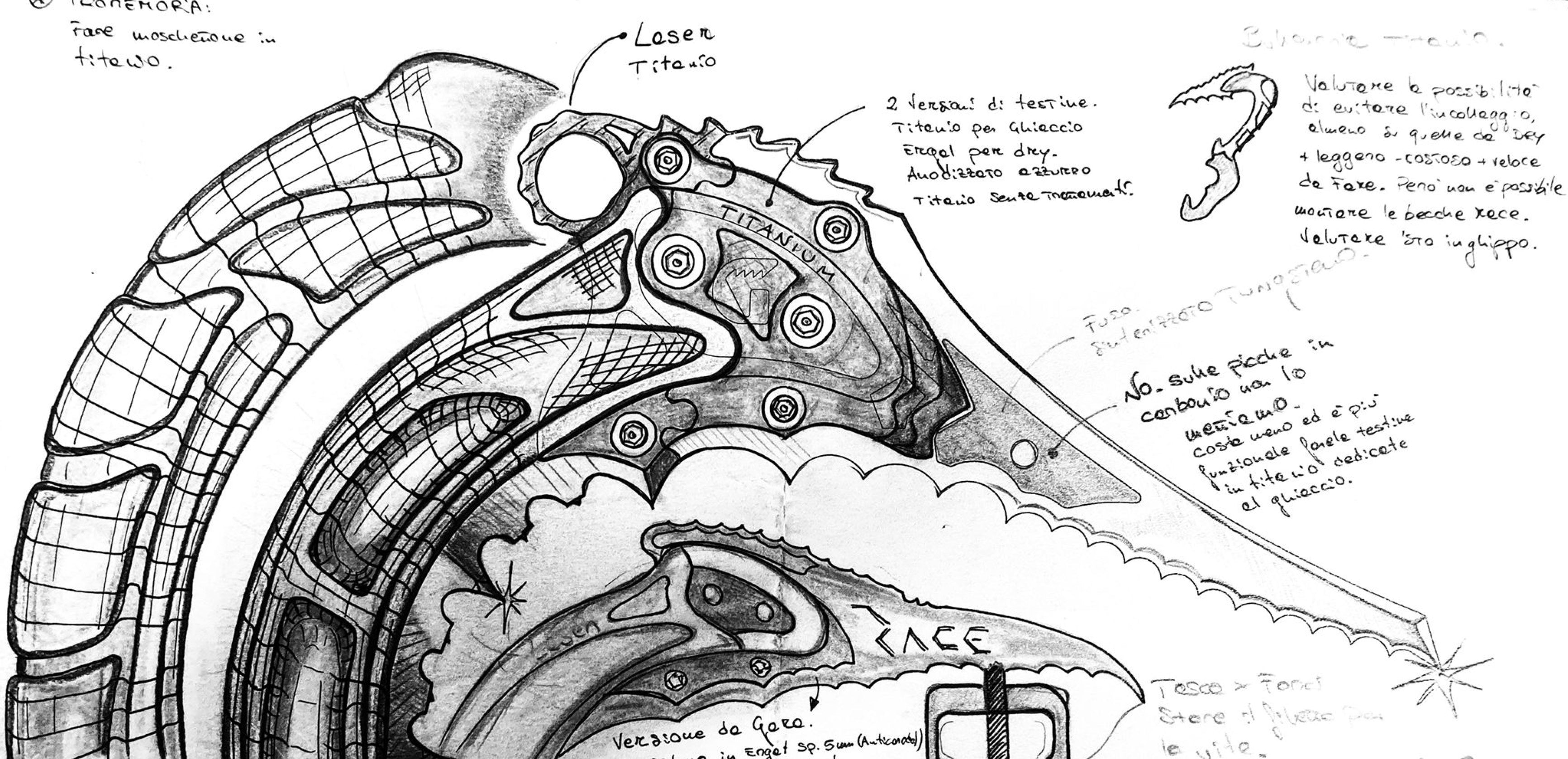
From the Murcielago to The Dark Machine and beyond by Stefano Azzali
Published on 23/02/2022
The path of research and development is never linear. We try to go forward, but sometimes we have to go back, swinging left and right, looking for the best passage. We start with ideas and often we are forced to change them, modify them, evolve them ... even distort them.
In our case, it is animated by the passion and desire to create the best products, and to always surpass ourselves.
This is the story of the latest generation of technical ice axes. A 20-year history, in seven stages. A story that is certainly not over yet.
Background - January 2002. Val Daone
I move a few steps to the right. I place my crampons and handcrafted ice axes on the ice slide that leads to the more vertical wall. I put a screw in, this is also handcrafted.
While I do this, something it touches my leg, it is Bibo, Placido's dog.
“I placed an ice screw where a dog has also climbed”.
With the suspicion of not being a vertical ice phenomenon, I reach the belay.
Bibo slipped down, using his nails in like Sylvester the cat for twenty meters but he is all right.
I had to improve, train hard, plan climbs in the cold and hours of gym … or improve the tools.
I chose to improve the tools, launching myself on a path that continues to this day.
Part 1 - 2003/2004: The Murcielago
In the very hot summer of 2003 I met Bubu Bole, one of the most prominent athletes at the time. I had emailed him a few days earlier with a couple of photos of the tools I had built and he was struck by the possibility of building tools with a complex shape. He was trying to transform into metal an idea he had been cultivating for some time: a competition tool that was not bound by the standards of mass production. We sit at the desk to design the tool of the new millennium.
Drawing a tool next to Bubu is like designing a motorcycle with Valentino Rossi, we dedicate a lot of time to each part of the tool.
I was surprised by Bubu's lack of interest in ice, he was looking for a tool for extremely overhanging walls, "the grades on ice are a closed system, the ice never overhangs and to train vertically you have to go up with skates". Over time I discovered that he was right, designing a tool for dry tooling is the best way to create a good tool for ice.

A few hundred hours of drawing and testing later, the first full ice axe made of composite material is a reality. Innovative shape, ergonomics on both grips, thin carbonkevlar grip, micro-alloy steel blade, titanium collar and head plates. Seeing it hanging in the shop amidst the competitors of the time, it looked like a Ferrari in a Twingo parking lot.They are used immediately in the world cup, the most severe terrain ever.

We derive information and use it to improve the product, continuously.

The following year, 2004, the tool is already completely new. We increase the volume of the shaft and grips, the blade is now modular and aluminum protections are added around the head. We optimize the grip for the reverse pulls. Passing from carbon kevlar to carbon, the tool acquires rigidity and the tensile strength goes from 500 to 1000 kg.


Part 2 - 2005: The FLAMINGO
Excited by the performance of the Murcielago, we then think of declining a version for ice, with the shape optimized to have the best possible swing. Thus the Flamingo was born.

The first pair of Flamingos were used by Ermanno Salvaterra on the north face of Cerro Torre, with titanium wings to float on the icy foam of the summit mushroom. We had made the drawing together a few months earlier on the table of the XII apostoli refuge, a comfortable corner in the lunar panorama of the southern part of the Brenta Dolomites, managed by Ermanno at the time. But this is another story!
The Flamingo became a very popular ice axe for many climbers, at all levels, while remaining a niche product with very limited productions. There are those who still use them and appreciate them today!
Part 3 - 2006-2010: The development of Murcielago and Flamingo
From the feedbacks coming from use in severe conditions, we continuously update the models.
These were the years of the first world titles won by athletes, of the homologations at the TUV in Munich, of the tests on the hardest dry tooling routes in the world and of the development of production techniques to meet the growing demands.
In 2009 the Murcielago Ergal arrives, born from two findings.
First, autoclave carbon molding does not allow mass production.
Second, full CNC milling is a faster and cheaper way to make complex shape tools.
For these tools, the piece is obtained from a plate of aeronautical aluminum, a bit like with sculptures, where the excess material is removed.
The strength of these tools is their extreme solidity. With the exception of the blade-shaft connection, the tool is integral, theoretically without weak points. Compared to carbon tools, however, they are heavier and less thermally insulated.
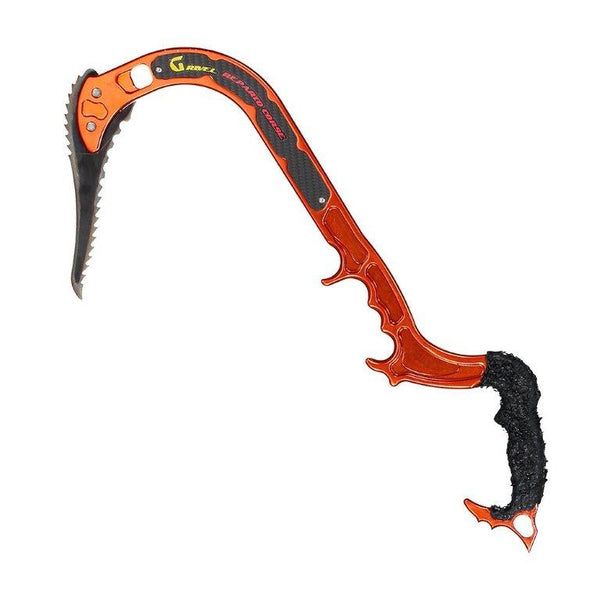


In 2010, from a photo on the Exocet route, it comes to my mind to design a tool dedicated to water ice, thin and with rock underneath. In this case, instead of favoring the swing, the angle between blade and the ice and the inclination of the grip are optimized. The idea is to replace the swing with a movement similar to that of "scratching" the ice, so as not to damage it when it was too thin to undergo the classic swings of the tools.

Thus was born the Master Alloy: aeronautical aluminum, carbon inserts to reduce vibrations, replaceable blade. Versatile tool, from mixed to ice to dry tooling, with blades dedicated to various terrains, very fast, simple and reliable blade change. Personal suggestion: the Master Alloys have always reminded me of the Lancia Delta Integrale (a sportscar fron the ‘80s): sharp-cornered, rigid, angry and imperfect on any terrain, but versatile and certainly “recent” even 30 years from now.

Part 4 - 2010-2016: The Grivel “Reparto Corse” (Racing Department)
In 2010 the adventure of the “Reparto Corse” (Racing Department) in Grivel begins, where they welcome me with a demanding welcome: "in the world there are at least 6 factories capable of producing red cars that go at 300 km per hour... Ferraris, however, are only made in Maranello".
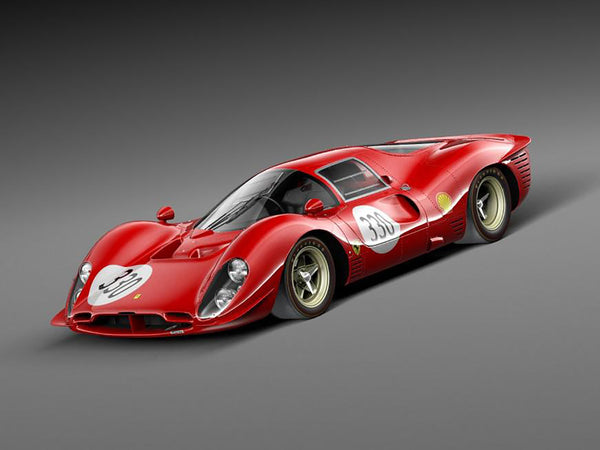
We “raised the volume” of the development of highly innovative tools with an R&D department that creates prototypes that can be used by world cup athletes but also by high-level mountaineers, committed to demanding projects and passionate about advanced materials.
As in the case of Ferrari cars, the products, in addition to being reliable and effective, must meet aesthetic requirements that make them immediately recognizable.

In the six years that the Racing Department has been operational, Grivel athletes have won 11 world titles out of 12 available.
In 2011 we began a search for alternative materials for the construction of the grips.
Steel (2011). The first is steel, with which we make the cheapest tool on the market, the X-Blade, with integral blade and shaft in micro-alloy steel. Basically indestructible and designed for mountain guides with several customers with them and to be the entry level tool with a high performance blade like the most expensive tools. One of the prototypes was in ballistic steel, if today we play with indestructible blades it is also thanks to the tests on this simple tool.
Magnesium (2012). Magnesium is the lightest of metals, specific weight 1.7 g / cm3, which compared to 2.8 for aluminum and 4.5 for titanium make it terribly fascinating. The Avatar is the first ice axe in the world to use magnesium, the Encelado is an evolution of the master alloys which with this material are lighter than carbon tools. Terribly expensive, difficult to manage and protect but super light. Will it be the weapon of the near future?

Unfortunately, only prototypes will remain, because you can’t win them all! We tested the magnesium ice axes with Angelika Rainer, multiple world champion able to understand a tool on the fly, they didn't work, too soft.Angelika Rainer, "Clash of the Titans", Helmcken Falls, ph Klaus Dell'Orto.
Titanium (2013). Titanium is a material with a specific weight that is halfway between aluminum and steel, it has a very high resistance to corrosion, so much so that it does not require any protection by painting or anodizing. Super resistant, "titanium is forever".
In addition to the accessories for the more expensive tools, it is possible to make shafts completely in titanium, the absorption of vibrations is optimal. But even here, they remain prototypes: the balance between functionality, manufacturability and economics is not found.

Avional (aeronautical aluminum, 2014). We have made the longest competition tools ever, with details dedicated to competitions, these tools had a "bite" to easily hold the axe in the mouth. In this case, aeronautical aluminum was the most suitable material.

Variable mass (2015). Ice axe with variable mass for mixed with hard ice sections, it had 50 grams of fishing sinkers running along the shaft, in the dry sections they were inside the shaft making the tool light in the head and easy to maneuver, on the sections of ice, when you need to swing, it was enough to bring the tool over the shoulder in the strike position and let the leads slide along the shaft to the head.
We did not continue for the noise of the weights sliding in the shaft which was annoying.

Part 5 - 2016-2017: Every cloud has a silver lining.
In 2016 a particular event happens: someone brings me a Murcielago broken during a competition, to understand what could have happened.
Playing with the pieces that remained intact, I slipped the grip into an old tube of the Grivel Quantum Race, coated in carbon, it fit perfectly.

Thus, from the breaking of a tool, the Comp Machines were born, a natural evolution of the Murcielago.

The tool uses increasingly heavier materials in the direction of the head. Carbon for the grip, light and thermally insulating, tubular aluminum on the shaft, forged aluminum head, steel lip. The "density" of the materials used increases towards the part that will impact on the ice.
The Comp Machine will never become a product, but it will remain an evolved prototype, used and appreciated by many athletes but without reaching the market. It needed an extra step ...Thomas Bubendorfer, ph Lorenzo Belfrond Photographia for Grivel
Part 6 - 2018: Dark Machine X and Dark Machine
The evolution of tools has always gone through misconceptions, abandoned prototypes and unrealizable solutions. The search for lightness, however, has remained constant over the decades; at the end of the 1980s the tools weighed more than 800 grams, in forty years we have halved the weight with steps of 10 grams at a time.
The tests on the most severe terrains remained constant, here below Gabriele Bagnoli tests his blades in ballistic steel on the hardest terrain. D15, a difficulty that 20 years ago was not even conceivable and where ergonomics and lightness are not a comfortable improvement, they are necessary to bear the loads on the hands.

Angelika Rainer on the hardest ice routes on the planet. Ph Nikki Smith.
The evolution of the Comp is the Dark Machine X, an optimized grip obtained made of carbon, a carbon-coated aeronautical aluminum tubular shaft to optimize weight and thermal insulation, forged head, special blades for dry tooling and ice.
Thus was born also the Dark Machine, with an optimized grip for ice climbing, less extreme than the Dark X, it facilitates swinging, extraction and control, and reduces weight compared to the X.
Every millimeter of this tool is studied and reasoned and the result is the perfect balance between hooking and striking, penetration and extraction.
10 years ago a tool to be acceptable had to weigh less than 650 grams, today the limit is 500 grams.
The Dark Machine weighs 490 grams, with a heavy blade, not filled with holes to cheat the scales. They adopt the Vario system to quickly configure the head (neutral, adze, light hammer, heavy hammer). We put everything we knew into it.
The Dark Machine and Dark Machine X are presented to the market at the ISPO in January 2019, and are available in stores since November 2019.
For the first time in this long story, we have now "industrial" products that have passed the artisanal/ pioneering phase and are mass-produced, in large quantities, certified according to standards, and sold all over the world. Despite the very high price, their success exceeds expectations.
Part 7 - 2019-2022: Towards the future, from the pandemic to Shakespeare
Since 2019, the special group "Tools of the future" is active within Grivel, dedicated to the development of these tools, from shapes to technologies to materials.
Sharing is fast, ideas circulate quickly. Drafts, projects, tests, photos, etc.
A small revolution, a reality in which improving the same product every year is part of the company itself.
2020 begins with doubts related to the possibility that the coronavirus epidemic could reach Europe. At the Ispo show in January we talk about nothing else, the fair with thousands of people from all over the world without a mask seems decades away, but only 24 months have gone by.
The new idea of a carbon tool was born in the lockdown weeks of spring 2020.
The day before putting my ideas on paper I went to the Ferrari museum in Maranello, there was Mansell's 1990 Formula 1 car, clean, essential, perfect even with the glasses fogged up by the mask.
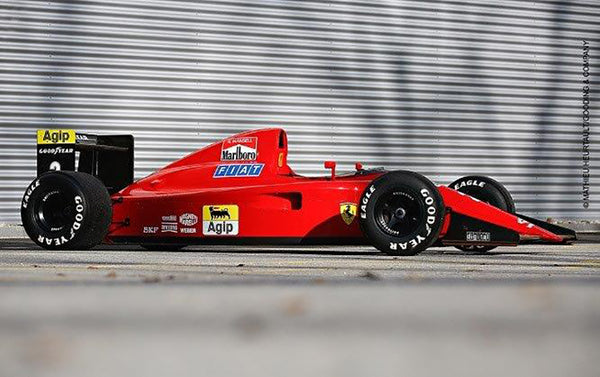
The new tool weighs 400 grams.
The concepts of the Dark Machine and Dark Machine X are taken to extremes: extreme lightness, high center of gravity and very close to the blade, minimal ergonomics of the grip.
The distance between this tool and the competition is the same that separates the chess from tic-tac-toe, the same as between Mansell's Ferrari and the Fiat “Uno” turbo.
Are we really going to make it? To be or not to be, that is the question!

For my job I try to join metal objects together, a kind of lego for adults.
I climbed for several years in the Dolomites managing to have fun without ever doing difficult things. Ice tools are my favorite playground, they are small and light enough to use expensive materials. Every season I annoy Grivel to make a new tool. I promise to continue.